Deutz-Fahr European tour shows the future of tractor manufacturing
11/01/2018
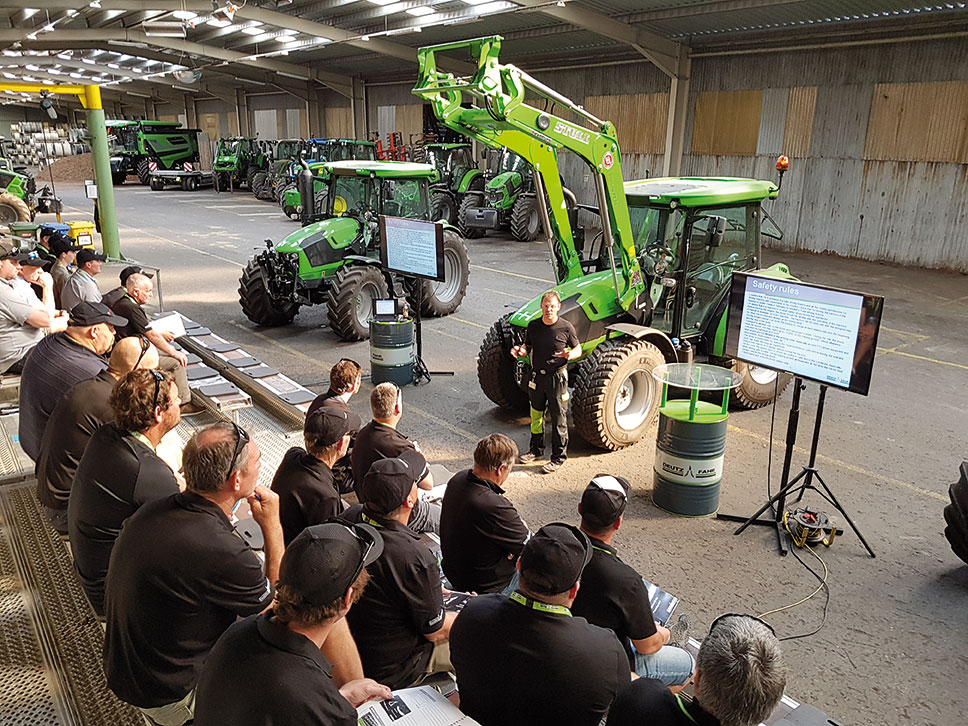
The Power Farming Euro Tour saw 63 New Zealand farmers, contractors and dealers hit Italy and Germany to see the latest tractor technologies from the SDF Group, which recently commissioned the most modern tractor factory in the world.
First stop was at the SDF headquarters in Treviglio, east of Milan in northern Italy. This is the home of Deutz-Fahr tractors up to 130hp and the capable and versatile Series 5 tractors. Guests could take in the heritage of a business that saw the Cassani brothers build their first diesel tractor in 1927, and the SAME DA, the world’s first 4WD tractor, launched in 1952. On the production line an upgrade is underway to produce automated guided vehicles (AGV) that carry the emerging tractors around the site and allow the factory to build up to 100 tractors each day.
Following a trip to a local dairy farm, which supplemented milk production with a large biogas plant, the party headed over the Alps to Munich and on to Lauingen, the home of Deutz-Fahr.
Said to be the fastest growing brand in Europe, Deutz-Fahr has recently commissioned a state-of-the-art tractor assembly plant aptly named Deutz-Fahr Land. In a building of 42,000 sqm on a site of 160,000 sqm and built at a cost of NZ$145 million, the mission is to build tractors right first time (RFT). A completed tractor leaves the production line every 12 minutes; the factory is said to be capable of producing up to 6,ooo units per annum on a one-shift basis.
Production centres on the Series 6, 7 and 9 tractors of 130-350hp. The RFT strategy is impressive given that a Series 9 tractor comprises over 5,000 individual parts (a premium car has 3,500-3,800 parts).
At the start of production, engine and transmission assemblies are carried on a line that passes through 20 workstations. Uniquely, workers travel on parallel moving conveyors said to reduce stress and mistakes during the process.
Once the Powertrain is completed it is subjected to a full hydraulic test on one of three rigs, using pneumatic pressure testing up to 220 bar, to ensure that quality is 100% before the units hit the paint-shop.
Prior to painting, dirt, dust and any silicones are removed, while an alkaline wash produces a keyed surface for the two automated painting robots. The paint process - said to have cost Euro 20m of the overall investment - combines application, heat curing and cooling before the final fit-out.
Interestingly, the final finish can endure 720 hours in the industry salt-spray test before signs of rusting appear. This contrasts with the car industry, where premium brands such as BMW or Mercedes are only able to endure about 240 hours.
After painting, the drive train meets the cabin assembly, body panels, wheels and tyres, before final accessories like drawbars, lighting and weight packs are added. Finally, the ability of the 90 workers to meet RFT is put to the test, with a rolling road test to ensure all functions operate properly.
And the final test? That involved a bunch of Kiwis taking the tractors to the paddock, using cultivators, harrows and heavily-laden trailers to see what RFT is all about.
Click here to learn more about Deutz-Fahr's tractors